Why Is My Keg Beer Not Carbonated Enough?
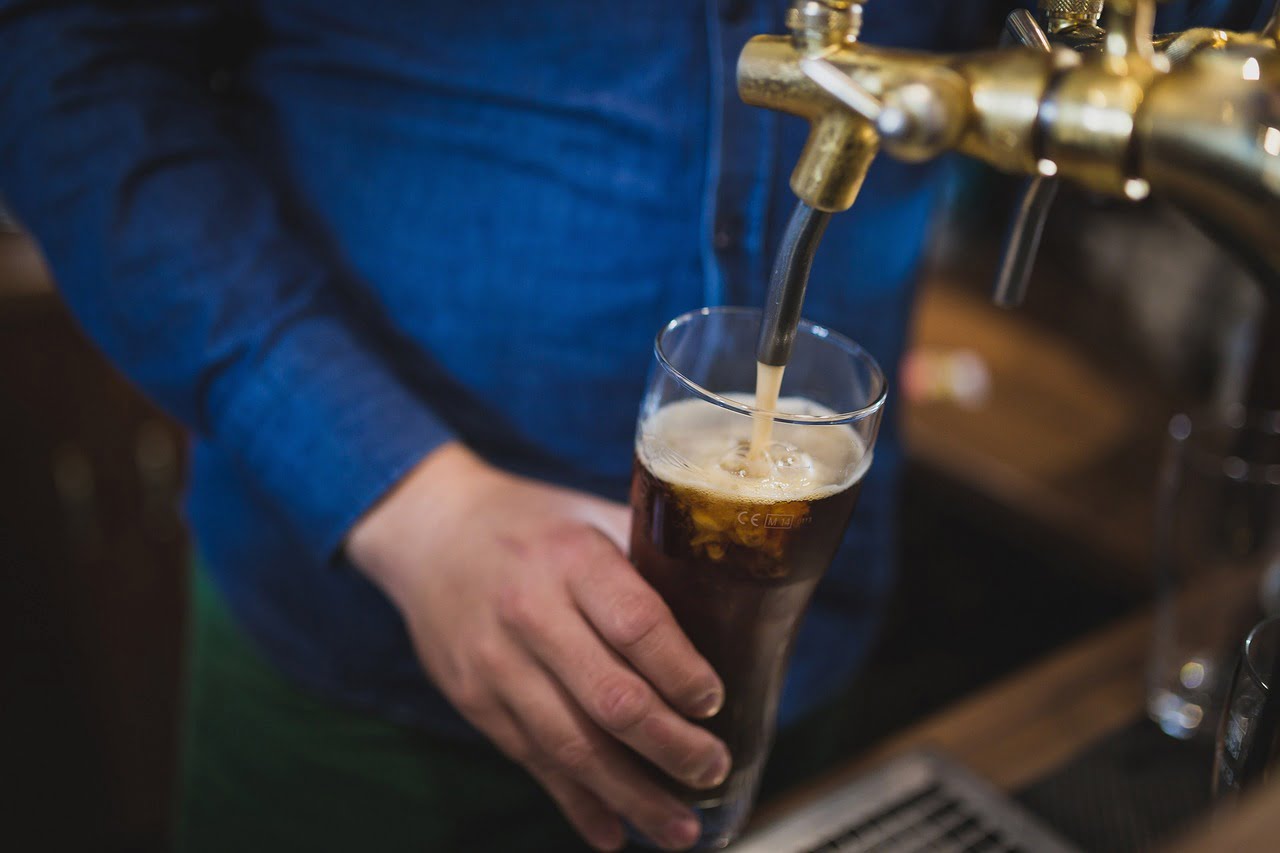
If you've recently tapped a keg and found the beer lacking in carbonation, you might wonder what went wrong. Before you assume it's a lost cause, consider this: there are some straightforward solutions that could bring those bubbles back to life. From checking your CO2 pressure to troubleshooting potential temperature issues, there are a few key areas to explore. But what if the problem lies beyond the obvious culprits? Stay tuned to uncover the lesser-known factors that might be affecting your keg's carbonation levels.
Inadequate CO2 Pressure
Have you checked if the CO2 pressure in your keg beer system is at the recommended level for proper carbonation? Inadequate CO2 pressure is a prevalent issue leading to insufficiently carbonated beer. The ideal range for carbonation typically falls around 10-12 psi for most beer styles. When the CO2 pressure is too low, the beer can turn out flat, lacking the desired effervescence and mouthfeel. To prevent this, it is crucial to ensure that your CO2 tank is set at the appropriate pressure using a regulator.
If you notice that your keg beer tastes flat, it might be due to the CO2 pressure being insufficient to properly carbonate the beer. This can happen if the pressure is set too low, causing the beer to lack the bubbles and carbonation levels expected for the style. Adjusting the CO2 pressure allows you to control the carbonation process, ensuring that your beer is carbonated to the desired level.
To resolve issues with flat beer, check the CO2 pressure and adjust it as needed to achieve the optimal carbonation level. Proper monitoring and maintenance of the CO2 pressure in your keg system are essential to guarantee that your beer is consistently carbonated and enjoyable to drink.
Improper Temperature Control
Improper temperature control is a critical factor that can significantly impact the carbonation levels of keg beer. Temperature control plays a crucial role in ensuring that your beer reaches its proper carbonation levels. When beer is stored or served at incorrect temperatures, it can lead to under-carbonated beer. Cold temperatures, in particular, can slow down the carbonation process, resulting in a less fizzy and lively brew.
To address this issue, it is essential to check and adjust the temperature settings of your kegerator. The kegerator should be set to maintain the ideal temperature for the type of beer you are serving. Different styles of beer may require slightly different temperature settings, so it's vital to consult the specific recommendations for the beverage in your keg.
Consistency is key when it comes to temperature control for carbonation purposes. Fluctuating temperatures can disrupt the carbonation process and lead to inconsistencies in the carbonation levels of your beer. By maintaining a steady and appropriate temperature throughout the storage and serving process, you can ensure that your keg beer achieves the proper carbonation expected for a satisfying drinking experience.
Incorrect Carbonation Level
To achieve the desired carbonation level in your keg beer, ensuring proper CO2 pressure application is essential. The pressure at which CO2 is applied to the keg plays a crucial role in carbonating the beer. If insufficient pressure is used, the beer may not become adequately carbonated. It is important to follow the recommended pressure levels based on the beer style and serving temperature to achieve optimal carbonation.
Additionally, allowing the beer sufficient time to absorb CO2 at the specified pressure is vital. Inadequate time for carbonation can lead to low carbonation levels in the beer. Proper temperature control during the carbonation process is also essential. Fluctuations in temperature can affect the ability of the beer to absorb CO2 effectively, resulting in under-carbonation.
Using the correct carbonation chart or calculations for the specific beer style and temperature is crucial. Incorrect calculations can lead to under-carbonation issues. Furthermore, ensuring the keg is properly sealed and that there are no leaks in the system is important. Any leaks or improper sealing can cause CO2 to escape, ultimately leading to insufficient carbonation of the beer. Paying attention to these factors will help you achieve the desired carbonation level in your keg beer.
Beer Line Length and Diameter
Ensure the appropriate length and diameter of your beer line to optimize carbonation levels in your keg beer. The beer line length and diameter play a crucial role in maintaining the desired carbonation level during dispensing. Longer beer lines offer increased resistance, which aids in achieving better carbonation levels as the beer flows through the system. On the other hand, a shorter beer line with a larger diameter can lead to a faster flow rate but might result in under-carbonated beer reaching your glass.
To ensure the ideal beer line length and diameter for your setup, factors such as the serving pressure and the desired carbonation level need to be taken into account. Adjusting the length and diameter of the beer line can help improve the carbonation of your keg beer. By finding the right balance between these variables, you can optimize the dispensing process and ensure that your beer maintains its carbonation levels from the keg to your glass.
Gas Leak in the System
Check for any gas leaks in your keg system by inspecting the CO2 tank connections, regulator, hoses, and keg seals for potential sources of escaping CO2. To address a potential gas leak in your keg system, follow these steps:
- Inspecting CO2 Tank Connections: Begin by checking the connections between the CO2 tank and the regulator. Ensure that the connections are secure and free of any visible damage. A loose connection or a damaged seal can lead to a gas leak, affecting the carbonation levels in your keg beer.
- Examining Regulator and Hoses: Inspect the regulator for any signs of leaks such as hissing sounds or visible gas escaping. Additionally, carefully examine all hoses connected to the keg system. Look for cracks, holes, or loose fittings that could be allowing CO2 to leak out.
- Checking Keg Seals with Soapy Water Solution: Apply a soapy water solution to the keg seals while the system is pressurized. Watch for bubbles forming at the seals, as this indicates a gas leak. Address any areas where bubbles appear by tightening the seals or replacing them if necessary to prevent CO2 from escaping and ensure proper carbonation levels in your keg beer.
Identifying and promptly fixing gas leaks in your keg system is crucial for maintaining the desired carbonation levels in your beer.